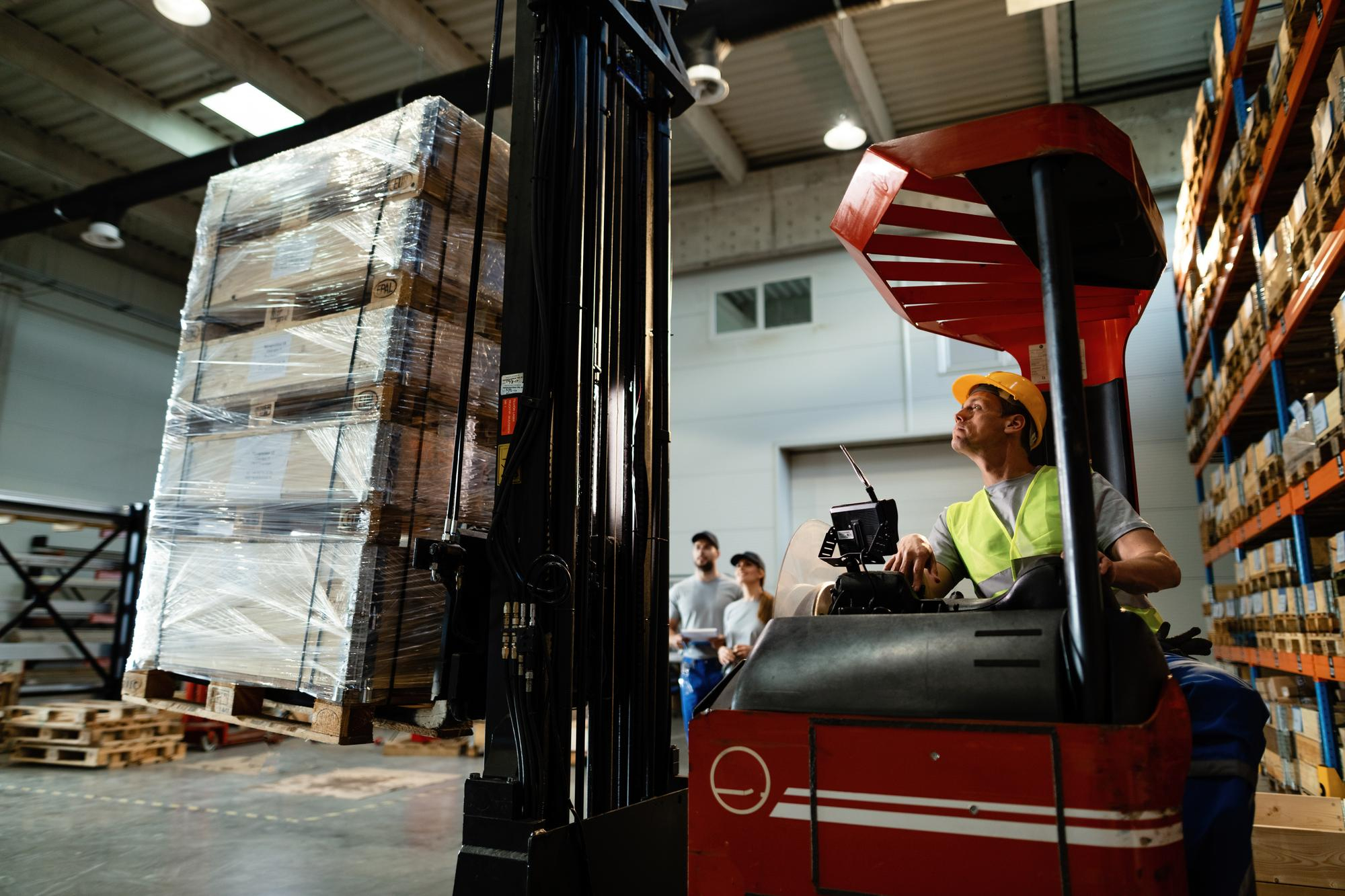
Un guide pratique sur l’optimisation des stocks grâce à un WMS - Warehouse Management System
Dans le contexte économique actuel, où la performance logistique devient un avantage concurrentiel majeur, la gestion optimale des stocks représente un enjeu stratégique pour les entreprises de toutes tailles. Face à des consommateurs de plus en plus exigeants en termes de délais de livraison et de disponibilité des produits, les organisations doivent repenser leurs approches traditionnelles de gestion d'entrepôt.
Les défis auxquels font face les entreprises sont nombreux et complexes. Les coûts de stockage représentent souvent entre 20 et 30% de la valeur des produits stockés, pesant significativement sur la rentabilité. Les ruptures de stock, quant à elles, peuvent entraîner des pertes de ventes immédiates et, plus grave encore, une détérioration durable de la satisfaction client. À l'inverse, le surstock immobilise inutilement de la trésorerie et augmente les risques d'obsolescence, particulièrement problématiques dans des secteurs comme l'électronique ou l'agroalimentaire.
C'est dans ce contexte qu'intervient le Warehouse Management System (WMS), une solution technologique qui révolutionne la gestion des entrepôts. Bien plus qu'un simple outil informatique, un WMS représente une véritable transformation dans la manière d'appréhender la gestion des stocks. En intégrant des technologies avancées et des algorithmes sophistiqués, il permet une orchestration précise et efficiente de l'ensemble des opérations d'entreposage, du réapprovisionnement à la préparation des commandes.
Cet article propose un guide pratique pour comprendre comment un WMS peut devenir le catalyseur d'une optimisation significative de la gestion des stocks. À travers une exploration détaillée des fonctionnalités essentielles, des meilleures pratiques de mise en œuvre, et des bénéfices concrets, vous découvrirez comment transformer vos défis logistiques en opportunités d'amélioration de la performance opérationnelle.
Sommaire :
1. Comprendre les fondamentaux d'un WMS
2. Les bénéfices concrets d'un WMS pour l'optimisation des stocks
3. Fonctionnalités avancées pour l'optimisation des stocks
4. Guide pratique de mise en œuvre
5. Retour sur investissement et métriques
6. Tendances futures et évolutions
Conclusion
Sources et Références
1. Comprendre les fondamentaux d'un WMS
Un Warehouse Management System (WMS) représente bien plus qu'un simple logiciel de gestion d'entrepôt. Il s'agit d'une solution complète qui orchestre et optimise l'ensemble des processus liés au stockage et aux mouvements des marchandises, depuis leur réception jusqu'à leur expédition.
Sur le plan technique, un WMS moderne s'articule autour d'une architecture centralisée qui communique en temps réel avec différents équipements et systèmes. Le cœur du système repose sur une base de données robuste qui maintient un référentiel précis des produits, des emplacements, et des mouvements. Cette base interagit avec plusieurs modules fonctionnels qui gèrent les différentes opérations de l'entrepôt, le tout accessible via des interfaces utilisateur intuitives, que ce soit sur des terminaux fixes ou mobiles.
Les fonctionnalités clés d'un WMS englobent la gestion des réceptions avec contrôle qualité intégré, l'optimisation des emplacements de stockage, la traçabilité complète des lots et numéros de série, la préparation des commandes avec optimisation des parcours, et la gestion des expéditions. Le système intègre également des fonctionnalités avancées comme la gestion des priorités, le réapprovisionnement automatique des zones de picking, et l'optimisation des ressources humaines et matérielles.
Une différence fondamentale entre un WMS et un module de gestion des stocks d'ERP réside dans sa spécialisation et sa granularité. Alors qu'un ERP se concentre sur la gestion administrative et financière des stocks au niveau macro, un WMS descend jusqu'au niveau le plus fin des opérations physiques. Il prend en compte les contraintes réelles de l'entrepôt comme la géométrie des zones de stockage, les caractéristiques des produits, ou encore les règles de prélèvement spécifiques.
Le cas de Leclerc Drive : Leclerc Drive a déployé le WMS Manhattan SCALE dans ses entrepôts. Cette implémentation leur a permis de réduire les erreurs de préparation de 80%, d'augmenter la productivité de 25% et d'atteindre une précision des stocks de 99,9%. Le système gère intelligemment les dates de péremption des produits frais et optimise les parcours des préparateurs en fonction des commandes en temps réel, illustrant parfaitement la puissance d'un WMS moderne.
2. Les bénéfices concrets d'un WMS pour l'optimisation des stocks
L'implémentation d'un WMS apporte des avantages tangibles qui transforment profondément la gestion des stocks. La visibilité en temps réel constitue l'un des bénéfices les plus immédiats. Chaque produit, chaque mouvement, chaque emplacement est tracé avec précision, offrant une vue d'ensemble instantanée de l'état des stocks. Cette transparence permet aux gestionnaires de prendre des décisions éclairées, d'anticiper les besoins et de réagir rapidement aux variations de la demande.
L'optimisation des emplacements et des mouvements représente un autre avantage majeur. Le WMS analyse en permanence les caractéristiques des produits, leur rotation, et les contraintes physiques de l'entrepôt pour suggérer les meilleurs emplacements de stockage. Cette optimisation dynamique réduit les distances parcourues, accélère les opérations de picking et minimise les manipulations inutiles, aboutissant à une amélioration significative de la productivité opérationnelle.
La réduction des erreurs constitue un bénéfice particulièrement impactant. Grâce aux contrôles systématiques et aux validations électroniques à chaque étape, le WMS diminue drastiquement les erreurs humaines. Les inventaires deviennent plus précis, les écarts se raréfient, et la fiabilité globale du stock s'améliore considérablement. Cette précision accrue se traduit directement par une diminution des coûts liés aux erreurs et une amélioration de la satisfaction client.
L'impact sur les KPIs de gestion des stocks est mesurable et significatif. Le taux de rotation des stocks s'améliore grâce à une meilleure organisation des flux. Le taux de service augmente grâce à une disponibilité optimisée des produits. Les coûts de stockage diminuent grâce à une utilisation plus efficiente de l'espace. Le temps de préparation des commandes se réduit grâce à l'optimisation des parcours et des process.
L’exemple Système U : Pour illustrer ces bénéfices, prenons l'exemple de Système U qui, après l'implémentation d'un WMS dans ses entrepôts régionaux, a constaté une réduction de 40% des erreurs de préparation, une augmentation de 15% de la productivité des opérateurs, et une amélioration du taux de service de 97% à 99,5%. Ces résultats démontrent comment un WMS peut transformer des objectifs d'optimisation en réalité opérationnelle mesurable.
3. Fonctionnalités avancées pour l'optimisation des stocks
Les fonctionnalités avancées des WMS modernes représentent une véritable révolution dans l'optimisation des stocks, en intégrant des technologies sophistiquées qui vont bien au-delà de la simple gestion d'inventaire.
Les algorithmes de prévision et de réapprovisionnement automatique constituent l'une des avancées les plus significatives. En analysant les historiques de vente, les tendances saisonnières, et même les événements externes comme les promotions ou les conditions météorologiques, ces systèmes peuvent anticiper avec précision les besoins futurs. Le WMS calcule automatiquement les points de commande optimaux et génère des suggestions de réapprovisionnement, permettant ainsi de maintenir un niveau de stock optimal qui équilibre disponibilité et coûts de stockage.
La gestion des dates de péremption et l'application des règles FIFO (First In, First Out) ou FEFO (First Expired, First Out) atteignent un niveau de sophistication inédit. Le système surveille en permanence les dates limites de consommation, priorise intelligemment les sorties de stock, et alerte proactivement sur les risques de péremption. Cette gestion fine permet de réduire significativement les pertes liées aux produits périssables tout en garantissant la fraîcheur des produits livrés aux clients.
Le cross-docking représente une autre fonctionnalité avancée particulièrement pertinente pour l'optimisation des flux. Le WMS identifie automatiquement les opportunités de transfert direct des marchandises de la zone de réception vers la zone d'expédition, sans passage par le stockage. Cette approche réduit les manipulations, accélère les flux, et minimise les besoins en espace de stockage.
L'intégration de l'intelligence artificielle et du machine learning ouvre de nouvelles perspectives fascinantes. Ces technologies permettent notamment d'affiner continuellement les règles d'allocation des emplacements en fonction des patterns réels d'utilisation, de prédire les paniers d'achat probables pour optimiser le picking, ou encore d'ajuster dynamiquement les priorités de préparation en fonction de multiples critères en temps réel.
Le cas de Carrefour : Pour illustrer ces capacités avancées, prenons l'exemple de Carrefour qui utilise un WMS intégrant l'IA dans ses entrepôts dark store. Le système analyse en temps réel plus de 200 variables pour optimiser la préparation des commandes e-commerce, résultant en une réduction de 30% des délais de préparation et une amélioration de 25% de la rotation des stocks, tout en maintenant une fraîcheur optimale des produits périssables.
4. Guide pratique de mise en œuvre
La mise en œuvre d'un WMS représente un projet stratégique qui nécessite une approche méthodique et rigoureuse. Cette transformation doit être orchestrée avec soin pour garantir son succès et maximiser le retour sur investissement.
Les étapes clés du déploiement commencent par une phase d'audit et de conception détaillée. Il est crucial d'analyser en profondeur les processus existants, d'identifier les points de friction actuels, et de définir précisément les objectifs d'optimisation. Cette phase permet également de cartographier l'ensemble des flux physiques et informationnels, servant de base pour la configuration future du système.
La préparation du déploiement constitue une phase critique. Elle implique la configuration minutieuse du système selon les spécificités de l'entreprise : paramétrage des règles de gestion, définition des processus opérationnels, création des profils utilisateurs, et mise en place des interfaces avec les systèmes existants. Un point d'attention particulier doit être porté sur la qualité des données de base (référentiel articles, cartographie de l'entrepôt, règles métier) car elles constituent le fondement de toute l'exploitation future.
La formation des équipes et la gestion du changement représentent des facteurs critiques de succès souvent sous-estimés. Il est essentiel d'impliquer les utilisateurs finaux dès les phases amont du projet et de mettre en place un programme de formation adapté à chaque profil : opérateurs, superviseurs, administrateurs système. La résistance au changement doit être anticipée et gérée par une communication transparente sur les bénéfices attendus et un accompagnement personnalisé.
L'intégration avec l'écosystème existant nécessite une attention particulière. Le WMS doit pouvoir communiquer de manière fluide avec l'ERP, le TMS (Transport Management System), et potentiellement d'autres systèmes comme les outils de e-commerce ou de CRM. Les interfaces doivent être robustes et les échanges de données parfaitement synchronisés pour éviter toute rupture dans la chaîne d'information.
Le déploiement WMS chez Decathlon : Decathlon France a réussi son déploiement WMS en adoptant une approche progressive : démarrage sur un site pilote, période de stabilisation, puis déploiement par vagues sur les autres sites. Cette stratégie leur a permis d'affiner les processus, de capitaliser sur les retours d'expérience, et d'atteindre leurs objectifs avec un taux de satisfaction utilisateurs de 92% dès la première année.
5. Retour sur investissement et métriques
L'évaluation du retour sur investissement (ROI) d'un projet WMS constitue un aspect fondamental pour toute organisation. Cette analyse doit prendre en compte non seulement les gains directs mais également les bénéfices indirects qui se manifestent à travers l'amélioration globale des opérations.
Le calcul du ROI d'un projet WMS s'articule autour de plusieurs composantes. Les coûts incluent l'acquisition du logiciel, l'infrastructure technique nécessaire, les frais de déploiement et de formation, ainsi que la maintenance annuelle. Face à ces investissements, les gains se manifestent à travers la réduction des coûts opérationnels, l'amélioration de la productivité, la diminution des erreurs, et l'optimisation des niveaux de stock. Un WMS bien déployé permet généralement d'atteindre un retour sur investissement entre 12 et 24 mois.
Les indicateurs de performance clés (KPIs) à suivre sont multiples et doivent être mesurés régulièrement. Au niveau opérationnel, on surveille particulièrement la précision des inventaires (objectif >99%), le taux de service (satisfaction des commandes), la productivité des opérateurs (nombre de lignes préparées par heure), et les temps de cycle (délai entre la réception d'une commande et son expédition). Au niveau financier, on analyse la rotation des stocks, le coût de possession des stocks, et le taux d'erreurs de préparation.
L'amélioration post-implémentation se mesure également à travers des métriques plus larges : la diminution des ruptures de stock, la réduction des stocks de sécurité, l'amélioration de l'utilisation de l'espace, et la baisse des coûts logistiques globaux. Un WMS performant permet typiquement une réduction de 20 à 30% des stocks de sécurité tout en maintenant ou améliorant le niveau de service.
Exemple de Chronopost : Pour illustrer ces concepts, prenons l'exemple de Chronopost qui, après l'implémentation d'un WMS dans son hub principal, a constaté un ROI en 18 mois avec une réduction de 40% des erreurs de tri, une augmentation de la productivité de 25% et une optimisation de l'espace de stockage de 15%. Ces résultats ont été obtenus grâce à un suivi rigoureux des KPIs et des ajustements continus basés sur l'analyse des données.
6. Tendances futures et évolutions
L’essor des solutions cloud et SaaS transforme la gestion des entrepôts en offrant une flexibilité accrue et une mise à jour continue des fonctionnalités. Contrairement aux systèmes traditionnels, ces solutions permettent une accessibilité en temps réel et une intégration simplifiée avec d’autres outils comme les ERP et les TMS. De plus en plus d’entreprises adoptent ce modèle pour réduire leurs coûts d’infrastructure et harmoniser leurs opérations sur plusieurs sites.
L’Internet des objets (IoT) et l’automatisation jouent également un rôle clé dans l’évolution des WMS. Grâce aux capteurs RFID et aux QR codes, chaque produit peut être suivi en temps réel, réduisant les erreurs et facilitant les inventaires. Associée aux robots autonomes (AGV, AMR), cette technologie permet d’accélérer le picking et d’améliorer la fluidité des flux logistiques. Par exemple, certains entrepôts de grande distribution utilisent ces robots pour optimiser la préparation des commandes et réduire les délais de traitement.
L’intelligence artificielle et le machine learning apportent une nouvelle dimension à l’optimisation des stocks en analysant les tendances de consommation et en ajustant automatiquement les niveaux de stock. Cette approche permet d’anticiper les ruptures et d’éviter le surstockage. Enfin, la blockchain commence à émerger comme un outil de traçabilité renforçant la sécurité et la transparence des flux de marchandises, notamment dans l’agroalimentaire et la pharmaceutique.
Avec ces avancées, le WMS devient un véritable centre de pilotage intelligent, capable d’optimiser en continu la gestion des stocks et d’améliorer la performance logistique des entreprises.
Sources et Références
Pour approfondir votre compréhension du sujet, nous vous recommandons de consulter les sources suivantes qui ont contribué à l'élaboration de cet article :
Rapports et Études :
- Oracle (2024) - "Présentation du système de gestion des entrepôts (WMS)" : https://www.oracle.com/sn/scm/logistics/warehouse-management/what-is-warehouse-management/
- Kaizen Institute (2023) - "L'importance de la gestion des entrepôts et des stocks" : https://kaizen.com/fr/publications/gestion-stocks-entrepot/
- Manhattan Associates (2024) - "Système de gestion d'entrepôt (WMS)" : https://www.manh.com/fr-fr/solutions/logiciel-de-gestion-supply-chain/systeme-gestion-entrepot
Articles Spécialisés :
- Mecalux (2023) - "L'analyse des données au service d'un WMS plus efficace" : https://www.mecalux.fr/articles-de-logistique/mustafa-cagri-analyse-donnees-wms
- Generix Group (2024) - "Comment utiliser le WMS pour une gestion d'entrepôt efficace" : https://www.generixgroup.com/fr-ca/blog/comment-utiliser-le-wms-pour-une-gestion-d-entrepot-efficace
- Shiptify (2023) - "WMS : la clé pour une gestion moderne des entrepôts" : https://www.shiptify.com/logtech/wms
Études de Cas
- Carrefour (2019) - "Artificial intelligence to optimise Carrefour’s supply chain" : https://www.carrefour.com/en/news/artificial-intelligence-optimise-carrefours-supply-chain?utm_source=chatgpt.com
- Manhattan Associates (2020) - "Decathlon modernise ses capacités d'entreposage pour son activité e-commerce en Chine avec Manhattan SCALE" : https://www.manh.com/fr-fr/notre-societe/articles-de-presse/communiques-de-presse/decathlon-modernise-ses-capacites-dentreposage-son